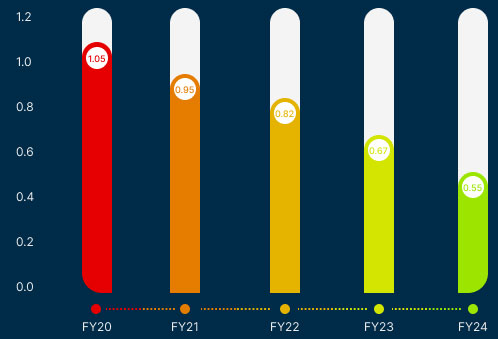
In COGD, H2 Generation plant 1000 NM3 of COG 250 NM3 of H2 is getting separated and remaining 550 to 750 NM3 gas sent back to TATA Steel network via Tail gas buffer due to high tar content.
By installing tail gas cleaning system at COGD plant which will clean the high tar content of COG gas. After that, 550 to 750 NM3 COG gas will be reused and fed to furnace that has reduced overall CO gas consumption
In FY20 water consumption was 1.05m3/Ton.
Recuse of wastewater by effective treatment.
Project identified to reduce specific water consumption from 1.1M3 /ton to 0.45 M3/ton out of which 0.55 M3/ton achieved